ما هي مضخة الطين الفائقة للطرد المركزي؟
Mar 11, 2025
ال مضخة الطين المركزي مضخة مركزية هو جهاز مهم في نظام مضخة الطين. فيما يلي مقدمة مفصلة لها:
ⅰ. التعريف والوظيفة
- التعريف الأساسي: عادةً ما تكون مضخة الشحن المركزية لضخ الطين في المضخة الطينية مضخة مساعدة صغيرة متصلة بخط الشفط مضخة الطين. وظيفتها الرئيسية هي إنشاء فراغ عن طريق تفريغ الهواء وملء المضخة بسائل الحفر. هذا يملأ مضخة الطين ، مما يتيح لها العمل بكفاءة ويوفر الضغط المطلوب لدورة طين الحفر.
- مبدأ العمل: تعمل على أساس مبدأ قوة الطرد المركزي. يتم تدوير المكره بسرعة عالية ، مما يولد قوة الطرد المركزي التي تتسبب في انتقال طين الحفر من مركز المكره إلى الحافة. تخلق هذه الحركة فرقًا في الضغط ، مع ضغط منخفض عند مدخل المكره والضغط العالي في المخرج. لذلك ، يتم امتصاص الطين من ميناء الشفط وتفريغه من المخرج تحت الضغط ، مع إدراك نقل طين الحفر.
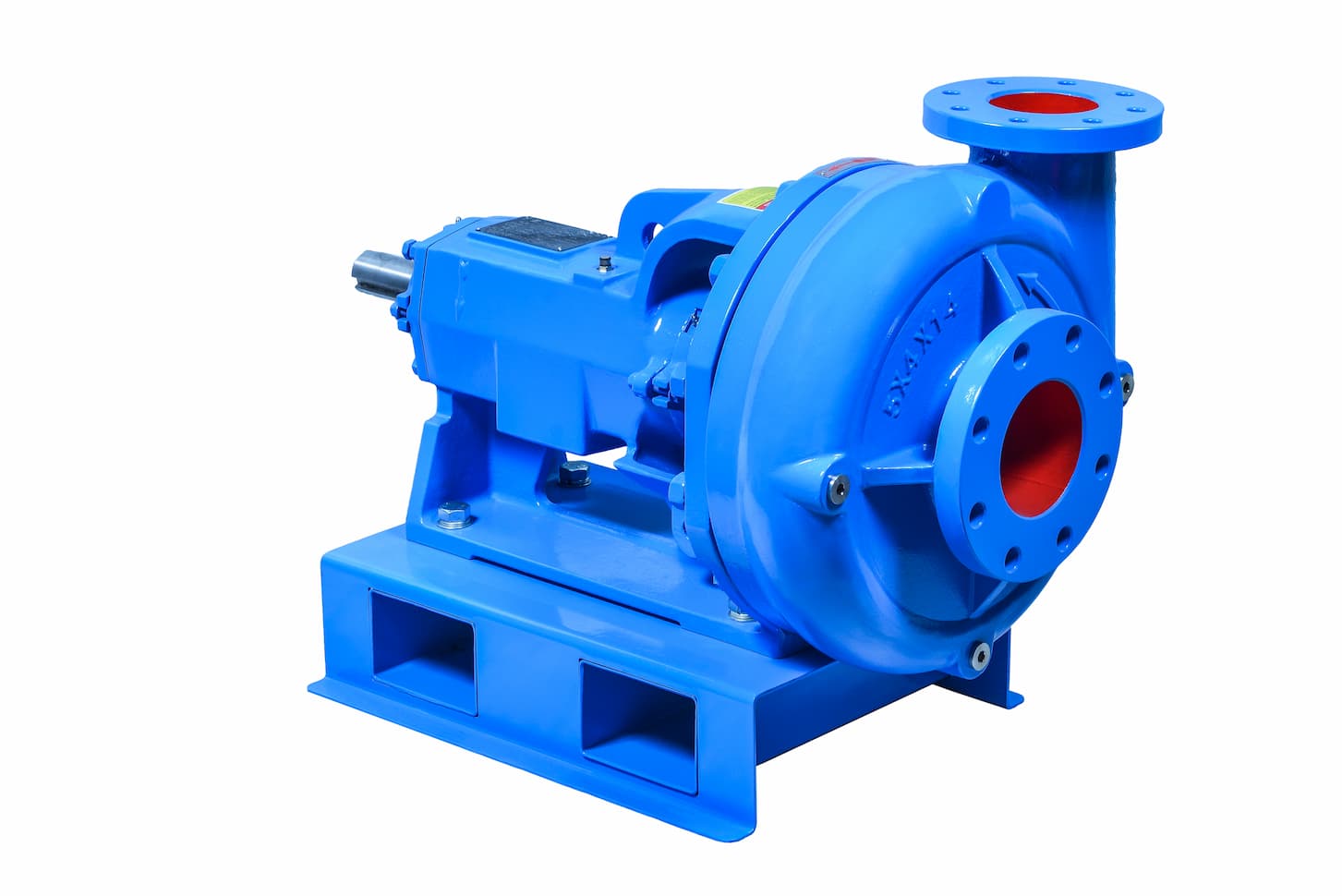
ⅱ. المكونات الرئيسية
- الطرد المركزي مضخة المكره: عادة ما يتم استخدام الدافع شبه المشترك أو الدافعين المغلقون. المكره شبه المصقول مناسب لنقل الطين الذي يحتوي على جزيئات معينة ، والتي يمكن أن تقلل من ارتداء الجسيمات على المكره ولديها قابلية جيدة ؛ يمكن للزمن المغلق تحسين كفاءة ورأس المضخة بشكل أفضل وهو مناسب للمناسبات ذات المتطلبات العالية لنقل الطين.
- مضخة غلاف: إنه مصنوع عمومًا من مواد مقاومة للارتداء ، مثل سبيكة الكروم العالية ، والحديد الزهر المقاوم للارتداء ، وما إلى ذلك ، لتحمل التآكل وارتداء الوحل. تم تصميم شكل غلاف المضخة كقناة تدفق حلزونية ، مما يسمح للطين بالتبادل تدريجياً في غلاف المضخة وتحويل الطاقة الحركية إلى طاقة الضغط لتحقيق الضغط على الوحل.
- ختم رمح: لمنع تسرب الطين والهواء من دخول المضخة ، يكون جهاز ختم العمود أمرًا بالغ الأهمية. تشمل أختام العمود الشائعة الأختام الميكانيكية وأختام التعبئة. تتمتع الأختام الميكانيكية بمزايا أداء الختم الجيد ، والتسرب الصغير ، وحياة الخدمة الطويلة ؛ تحتوي أختام التعبئة على خصائص البنية البسيطة والتكلفة المنخفضة والصيانة المريحة.
- المحامل: يتم استخدامها لدعم عمود المضخة وضمان دقة الدوران واستقرار عمود المضخة. نظرًا لأن مضخة الشحن الفائقة في مضخة الطين قد تحمل قوى شعاعية ومحورية كبيرة أثناء التشغيل ، عادة ما تحتاج المحامل إلى سعة حمولة عالية الحمل ومقاومة التآكل.
ⅲ. الميزات الهيكلية
- مواد مقاومة للارتداء: نظرًا لغطاء طين الحفر ، فإن مكونات المضخة في ملامسة الطين ، مثل المكره وغلاف المضخة ، عادة ما تكون مصنوعة من مواد مقاومة للارتداء مثل سبيكة الكروم العالية وحديد الدكتايل المقاوم للارتداء. هذا يعزز مقاومة التآكل للمضخة ويطيل عمر خدمتها.
- تزييت الشحوم: عادة ما يتم تشحيم محامل المضخة مع الشحوم. يمكن أن تقلل طريقة التزييت هذه من الاحتكاك والارتداء بين المحمل والعمود ، مما يضمن التشغيل السلس للمضخة ومناسبة لظروف العمل حيث تحتاج المضخة إلى العمل بشكل مستمر لفترة طويلة.
ⅳ. المزايا
من حيث الهيكل والتركيب
- بنية بسيطة ومدمجة: عادة ما تتكون مضخة الشحن الخارق لمضخة الطين من مكونات رئيسية مثل جسم المضخة ، المكره ، والعمود. الهيكل العام بسيط نسبيًا ، دون أجهزة نقل معقدة أو هياكل متعددة الكامبر.
- سهولة التثبيت: يعتمد تصميم بنية خط أنابيب ، مع المدخل والمنفذ على نفس الخط المستقيم. أثناء التثبيت ، يجب أن يتم رست فقط المدخل والمنفذ. يمكن تثبيته مباشرة في سلسلة مثل خط أنابيب ، واحتلال مساحة أرضية صغيرة.
من حيث الأداء والتشغيل
- عالية الكفاءة: مع تصميم المكره المتقدم والهيكل الداخلي المحسّن ، يمكنه تحويل الطاقة الميكانيكية للمحرك بكفاءة إلى طاقة الضغط والطاقة الحركية للطين ، مع الحفاظ على كفاءة عمل عالية في ظل ظروف العمل المقدرة.
- التشغيل المستقر: تضمن التركيز المطلق لعمود المضخة والتوازن الديناميكي والثابت الممتاز للبث أن تكون المضخة لديها اهتزاز صغير وضوضاء منخفضة أثناء التشغيل. على سبيل المثال ، عند تشغيل مضخة الطين ، لن تنتج اهتزازات وضوضاء كبيرة ، مما يوفر بيئة عمل جيدة.
- تنظيم التدفق المريح: يتناسب التدفق بشكل مباشر مع السرعة الدورانية ، ويمكن تعديل التدفق بسهولة من خلال آلية تغيير السرعة أو محرك تنظيم السرعة ، مما يتيح التعديل المرن لحجم نقل الطين وفقًا لظروف العمل الفعلية.
- القدرة القوية للذات: بشكل عام ، لديها قدرة معينة على الانتشار الذاتي. قبل البدء ، ليست هناك حاجة إلى كمية كبيرة من عمليات التحضير مثل بعض أنواع المضخات الأخرى. يمكن أن يؤدي بسرعة إلى تصريف الهواء في أنبوب الشفط ويدرك الشفط السلس للطين.
من حيث الصيانة والتشغيل
- العملية البسيطة: العملية بسيطة نسبيًا ، وعمليات البدء والإيقاف مريحة نسبيًا ، دون إجراءات التشغيل المعقدة والمهارات المهنية. ولا يتطلب مراقبة وضبط متكررة أثناء التشغيل ، مما يجعل من السهل تحقيق الأتمتة والتشغيل عن بُعد.
- تكلفة الصيانة المنخفضة: الهيكل البسيط يجعل الصيانة والإصلاح تعمل سهلة نسبيًا ، كما أن استبدال الأجزاء مريح نسبيًا. على سبيل المثال ، عند استبدال الأجزاء الضعيفة مثل المكره وختم مضخة الطين أثناء الصيانة ، ليست هناك حاجة لتفكيك عدد كبير من الأجزاء ، مما يقلل من تكلفة الصيانة ووقت الإصلاح.
ⅴ. عند اختيار نموذج مناسب لمضخة الشحن المركزية لمضخ الطين ، يجب النظر بشكل شامل في عوامل متعددة. فيما يلي النقاط الرئيسية المحددة:
الخصائص المتوسطة
- اللزوجة: سوف تؤثر اللزوجة العالية للطين على أداء وكفاءة المضخة ، مما يقلل من رأس وتدفق المضخة. للطين مع لزوجة أكبر من 500MPa・S ، يُنصح بمضخة الشحن الفائقة الطرد المركزي مع المكره الكبير للمرور وسرعة الدوران المنخفضة لتقليل مقاومة التدفق ومنع الانسداد.
- محتوى المواد الصلبة: الطين مع محتوى المواد الصلبة العالية هو كاشف للغاية للمضخة. عندما يكون محتوى الرمل أقل من 15 ٪ ، يمكن استخدام مضخة مصنوعة من مواد الحديد الزهر العادية ؛ عندما يتراوح محتوى الرمل بين 15 ٪ و 40 ٪ ، يلزم وجود مواد مقاومة للارتداء مثل سبيكة الكروم المرتفعة ؛ عندما يتجاوز محتوى الرمل 40 ٪ ، ينبغي النظر في مضخة مصنوعة من الفولاذ المقاوم للصدأ المزدوج أو مع طلاء كربيد التنغستن على السطح.
- التآكل: إذا كان الوحل تآكلًا ، مثل احتواء الأحماض والقلويات والمواد الكيميائية الأخرى ، فيجب اختيار مضخة مصنوعة من مواد مقاومة للتآكل ، مثل سبيكة التيتانيوم المبطنة بالبلاستيك ، وما إلى ذلك ، لتمديد عمر خدمة المضخة.
متطلبات التدفق والرأس
- التدفق: حدد تدفق النقل الطيني المطلوب وفقًا للاحتياجات الهندسية الفعلية ، بشكل عام في متر مكعب في الساعة (M³/ساعة). على سبيل المثال ، في عمليات التعدين على نطاق واسع ، قد يكون هناك حاجة إلى تدفق لمئات الأمتار المكعبة في الساعة. يجب أن يكون التدفق المقنن للمضخة المحددة أكبر قليلاً من التدفق الفعلي المطلوب للتأكد من أنه يمكن تلبية متطلبات النقل في ظل ظروف عمل مختلفة.
- الرأس: يشير الرأس إلى الارتفاع الذي يمكن للمضخة رفعه بالطين ، بالأمتار (م). يجب حساب الرأس المطلوب وفقًا لعوامل مثل مسافة النقل ، وفرق الارتفاع ، ومقاومة خطوط الأنابيب. على سبيل المثال ، عند نقل الطين من تحت الأرض إلى الأرض ، إذا كان الارتفاع الرأسي 100 متر ، وبالنظر إلى احتكاك خط الأنابيب والخسائر الأخرى ، فقد تحتاج مضخة برأس 120-150 مترًا.
بيئة العمل
- الحد من المساحة: إذا كانت مساحة التثبيت محدودة ، كما هو الحال في بعض العمليات تحت الأرض أو محطات معالجة مياه الصرف الصحي الصغيرة ، يمكن اختيار مضخة الشحن المركزية لضخ الطين الرأسي ، والتي تحتل مساحة صغيرة في الأرضية ؛ في مساحة مفتوحة ، مثل منطقة التشغيل في الهواء الطلق لمنجم كبير ، تعد المضخة الأفقية أكثر ملاءمة للتركيب والصيانة.
- درجة الحرارة والرطوبة: في بيئة عالية الحرارة ، تحتاج المواد والأختام للمضخة إلى مقاومة عالية درجة الحرارة ؛ في بيئة غاز رطبة أو تآكل ، ينبغي النظر في الأداء المقاوم للرطوبة ومضاد للتآكل للمعدات الكهربائية للمضخة.
السلطة والسيطرة
- مصدر الطاقة: هناك طرق تعتمد على الطاقة والمحفزة بالديزل. تعتمد على الطاقة مناسبة للأماكن ذات إمدادات الطاقة الخاصة بشبكة الطاقة المستقرة ، مع مزايا انخفاض تكلفة التشغيل والكفاءة العالية ؛ تعتمد على الديزل مناسبة للمناطق الحقل أو النائية دون تغطية شبكة الطاقة ، مثل عمليات الاستكشاف الجيولوجي الميداني.
- وضع التحكم: حدد مضخة مع التحكم اليدوي أو التحكم التلقائي أو التحكم عن بُعد وفقًا للاحتياجات الفعلية. يمكن للتحكم التلقائي والتحكم عن بُعد تحقيق المراقبة في الوقت الحقيقي وتعديل حالة تشغيل المضخة ، وتحسين كفاءة العمل ومستوى الأتمتة ، وهي مناسبة للمشاريع الهندسية على نطاق واسع أو أماكن غير مراقبة.
عوامل أخرى
- تكلفة الصيانة: تشمل تكلفة الاستبدال للأجزاء الضعيفة ، وصعوبة الصيانة ، وما إلى ذلك. اختيار المضخة بهيكل بسيط وعالمية قوية من الأجزاء الضعيفة يمكن أن يقلل من تكلفة الصيانة وصعوبة ، وتقصير وقت الصيانة ، وتحسين كفاءة التشغيل للمعدات.
ⅵ. صيانة مضخة الطرد المركزي لمضخة الطين
1. الصيانة
تتضمن صيانة وصيانة مضخة الطرد المركزي للطرد المركزي جوانب متعددة مثل الفحص اليومي والصيانة المنتظمة وصيانة المكونات الرئيسية. فيما يلي الطرق المحددة والنقاط الرئيسية:
مراقبة حالة العملية
- الضغط والتدفق: راقب عن كثب ضغط المدخل والمخرج وتدفق المضخة لضمان عملها بشكل ثابت ضمن نطاق المعلمة المقدرة. قد تشير التقلبات غير الطبيعية في الضغط أو التدفق إلى مشاكل مثل الانسداد أو التسرب أو تلف المكون داخل المضخة.
- درجة الحرارة والاهتزاز: تحقق من درجة حرارة جسم المضخة والمحامل والمحرك لمنع ارتفاع درجة الحرارة. بشكل عام ، يجب ألا تتجاوز درجة حرارة تحمل 70 ℃ ، ويجب ألا تتجاوز درجة حرارة المحرك القيمة المحددة على اللوحة. في الوقت نفسه ، انتبه إلى حالة الاهتزاز أثناء تشغيل المضخة. قد يشير الاهتزاز غير الطبيعي إلى أن عمود المضخة غير محدد ، أو المكره غير متوازن ، أو أن الأساس فضفاض.
- الصوت: مضخة التشغيل عادةً تحتوي على صوت مستقر وموحد. في حالة حدوث الضوضاء غير الطبيعية ، مثل أصوات الاحتكاك ، أو أصوات التأثير ، أو أصوات التجويف ، توقف الجهاز فورًا لفحصه لتحديد ما إذا كان هناك تآكل مكون أو رفاهية أو ظواهر التجويف.
فحص المظهر
- حالة التسرب: تحقق مما إذا كان هناك تسرب من الطين في جسم المضخة ، وأجزاء توصيل خط الأنابيب ، والأختام. قد يكون التسرب الطفيف بسبب التآكل أو التثبيت غير السليم للأختام ، وقد يؤدي التسرب الشديد إلى انخفاض في أداء المضخة أو حتى الضرر ، والذي يجب التعامل معه في الوقت المناسب.
- سلامة المكون: تحقق من ظهور المضخة للتأكد من عدم تالف جميع المكونات ، وليس فضفاضة ، وأجهزة الحماية كاملة وفعالة. إذا تم العثور على البراغي لتكون فضفاضة ، فقم بتشديدها في الوقت المناسب ؛ إذا كانت هناك تشققات أو تلف الغلاف ، فقم بتقييم التأثير على أداء المضخة وإصلاحه أو استبداله في الوقت المناسب.
2. الصيانة الجماعية
التنظيف والتزييت
- التنظيف: تنظيف بانتظام بقع الطين والغبار والزيت على سطح جسم المضخة لمنع تراكمها من التأثير على تبديد الحرارة وتآكل جسم المضخة. بالنسبة إلى مصفاة الشفط ، قم بتنظيفه بشكل متكرر لتجنب عدم كفاية تدفق الشفط الناجم عن انسداد مصفاة ، مما قد يؤدي إلى مشاكل مثل التجويف.
- تزييت: وفقًا لمتطلبات دليل المعدات ، أضف أو استبدال زيت التشحيم بانتظام للأجزاء الدوارة مثل المحامل. بشكل عام ، بالنسبة للمحامل المشحمة بزيت التشحيم ، يجب استبدال زيت التشحيم كل 2000-3000 ساعة من التشغيل ؛ بالنسبة للمحامل التي تشبه الشحوم التشحيم ، يجب تجديد الشحوم التشحيم كل 1000-1500 ساعة من التشغيل.
اختبار الأداء وتعديله
- اختبار الأداء: اختبر أداء المضخة ، بما في ذلك المعلمات مثل التدفق والرأس والكفاءة ، على فترات منتظمة (مثل كل 3-6 أشهر) ، وقارنها ببيانات الأداء الأصلية لتقييم تغييرات الأداء للمضخة. إذا انخفض الأداء بشكل كبير ، فقم بتحليل الأسباب وتنفيذ الصيانة والتكيف.
- التعديل: قم بإجراء التعديلات اللازمة للمضخة وفقًا لنتائج اختبار الأداء. على سبيل المثال ، من خلال ضبط الخلوص بين المكره وغلاف المضخة ، يمكن تحسين أداء المضخة ؛ للمضخات باستخدام تنظيم سرعة التردد المتغير ، اضبط تردد المحرك وفقًا للاحتياجات الفعلية لتحسين ظروف تشغيل المضخة.
3. Key -component صيانة
المكره ومضخة الغلاف
- التفتيش: تحقق بانتظام من حالة التآكل من المكره وغلاف المضخة ، وخاصة شفرات المكره وأجزاء قناة التدفق في غلاف المضخة. إذا تجاوز تآكل المكره الحد المحدد ، فسيؤدي ذلك إلى انخفاض في تدفق المضخة ورأسه ، ويجب استبداله في الوقت المناسب. بالنسبة لحالة التآكل الطفيف ، يمكن اعتماد تقنيات الإصلاح مثل الطلاء المقاوم للارتداء.
- علاج التآكل: إذا كانت الوسيلة تآكلًا ، فانتبه إلى حالة التآكل من المكره وغلاف المضخة. عند العثور على علامات التآكل ، يمكن اتخاذ تدابير مثل الطلاء المضاد للتآكل واستبدال المواد المقاومة للتآكل.
جهاز الختم
- الختم الميكانيكي: تحقق من حالة التآكل من الختم الميكانيكي ولاحظ ما إذا كانت هناك خدوش أو تشققات أو تشوهات على سطح الختم. بشكل عام ، تبلغ عمر خدمة الختم الميكانيكي 8000-12000 ساعة. عندما يتم الوصول إلى عمر الخدمة أو حدوث مشاكل مثل التسرب ، يجب استبداله في الوقت المناسب. في الوقت نفسه ، تأكد من أن نظام سائل التدفق للختم الميكانيكي يعمل بشكل طبيعي لضمان تبريد وتزييت سطح الختم.
- ختم التعبئة: تحقق بانتظام من حالة التآكل والشيخوخة في التعبئة ، وضبط ضيق الغدة التعبئة في الوقت المناسب لضمان تأثير الختم. عندما تكون كمية التسرب من التعبئة كبيرة جدًا ، يجب استبدال التعبئة.